An Encoder is a device used to change one format of data to another. In other words, a device that is used to detect & change mechanical motion into an analog coded or digital coded o/p signal. Encoders are available in two configurations like linear & rotary, but the most frequently used configuration is rotary. So, a rotary encoder is designed in two basic forms like the absolute encoder and the incremental encoder.
Most rotary encoders are designed with a plastic or glass slotted disk because radial lines within every track will disrupt the beam in between a photoemitter-detector pair to generate digital pulses. This article discusses an overview of a rotary encoder and its working with applications.
What is Rotary Encoder?
A rotary encoder (shaft encoder) is an electro-mechanical device, used to change the motion of a shaft, angular position of a rotary shaft. This encoder generates an electrical signal based on the rotating movement like either analog or digital.
These are used in a variety of applications where control or monitoring is required like robotics, industrial controls, photographic lenses, input devices of computers like trackballs, optomechanical mice, controlled stress rheometers, etc.
The rotary encoder construction can be done by using different parts like encoder shaft, code disc or rotary disc including labels, source of light including electronic board, receiving IR photosensor, Optical-mechanical block including gears, electronic board with digital interface converters & signal processors.
Rotary Encoder Working
In the rotary encoder, we can observe that how the square wave signals are generated. Generally, this encoder includes a disk, spaced evenly with contact zones. The connection of these contact zones can be done to the common pin-C & other two separate contact pins like A & B shown below.
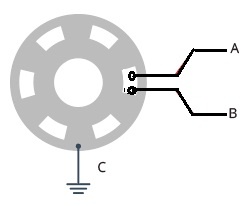
The disk in this encoder will start revolving slowly and both the pins like A & B will be in contact through the common pin. Thus, the generation of two square wave output signals can be done accordingly.
Here, the rotating position can be determined by using any of the two outputs. But, if we want to decide the direction of rotation, then we have to consider both signals simultaneously.
We can observe that the two o/p signals are moved at 90 degrees out of phase from each other. If this encoder is turning in a clockwise direction, then output A will be after output B.
Every time, if we count the steps, then the signal will be changed from Low to High or High to Low. At that time, we can observe the two output signals like A & B will have reverse values.
If this encoder is revolving counter-clockwise, then both the output signals will have identical values. By considering this, we can simply program the controller to study the position of the encoder & the direction of rotation.
Rotary Encoder Types
These encoders are classified into two types which include the following.
- Incremental Type
- Absolute Type
Incremental Rotary Encoder
The incremental rotary encoder is used to provide a sequence of low & high waves. These waves will specify the movement of position. These types of encoders will provide a sequence of periodic signals within the pulses form because of the shaft revolution motion.
An object’s speed can be measured through pulse counting for some time. These pulses can be simply counted from a reference point to determine the position otherwise distance covered.
The incremental rotary encoder generates two digital o/p signals where the phase relationships among these two sensors will decide whether the encoder’s shaft is revolving clockwise direction otherwise anti-clockwise. So by using this encoder, the position can be simply determined.
Once the light-emitting diode produces the light, then it will transmit through a crystal clear disk. Once this light signal receives by a photosensor then a sinusoidal signal can be generated, which is changed into a pulse train or square wave. The pulse wave can be transmitted toward the rotary counter which will transmit the signal to generate the preferred function.
Absolute Rotary Encoder
An absolute rotary encoder is used to maintain the positions information once power is detached from the rotary encoder. This encoder’s position is instantly available once power is provided.
This encoder includes different code rings through different binary weightings which provide a data word for signifying the rotary encoder’s absolute position in a single revolution. So this type of encoder is also called a parallel absolute encoder.
An absolute rotary encoder with multi-turn mainly comprises extra gears & code wheels. A wheel with high resolution can measure the fractional rotation lower-resolution and geared code wheels with lower resolution can record the shaft’s complete revolutions.
Advantages
The advantages of a rotary encoder include the following.
- These are reliable
- Accurate
- Resolution is high
- Size is compact
- Less cost feedback
- Integrated electronics
- Can be included in existing applications
The disadvantages of a rotary encoder include the following.
- It is vulnerable to oil, dirt & contaminants of dust.
- The interface of the direct light source.
Applications
The applications of rotary encoder include the following.
- These are used where speed, direction, acceleration, and monitoring rotation rate are required.
- These are used in different industries like material handling, packaging & conveyor.
- In the automation field, these encoders are utilized as sensors for speed, angle, acceleration & position.
- These are used to measure linear motion by using gear racks, spindles, cable pulls, or measuring wheels.
- These encoders are used to change a mechanical input to electrical signals by using tachometers, counters, PLC systems & PCs in industries.
- These are used in packaging, assembly machines, indication systems, printers, CNC machines, testing machines, robotics, textiles, motor feedback, medical equipment, drilling, and labeling machines.
What is an Absolute Encoder?
An absolute encoder is used to provide a unique position value of shaft or data word at each point of revolution to represent the “absolute” position of the encoder. These encoders are available in either single-turn or multi-turn. Single-turn encoders are used where position verification is needed whereas multi-turn encoders are used for lengthy or complex positioning-based applications.
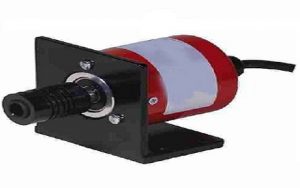
This encoder also retains the information on the current position when the power supply is detached from the encoder. The encoder position is accessible instantly once the power supply is given. This encoder includes different code rings through a variety of binary weightings which supply a data word signifying the encoder’s absolute position in a single revolution. So this kind of encoder is frequently called a parallel absolute encoder.
Working Principle
The absolute encoder working principle is, when the shaft rotates, it works by generating a digital word of bit. There are two discs including concentric rings through offset markers. Here, one disc is connected to the central shaft whereas the other moves freely.
Once the disc rotates, then the markers through the path of this encoder will adjust the fixed disc’s position. Every arrangement with an absolute rotary encoder disc signifies a unique binary code. The binary code in this encoder will determine the complete position of the object.
Absolute Encoder Types
There are different types of absolute encoders available which include the following.
Organic Solid Core Absolute Encoder
The organic solid core type is designed with carbon brushes. Its solid resistor body is wide, so it provides a longer mechanical life as compared to a binary encoder. The main function of this encoder is to adjust voltage & current within highly reliable, high wear resistance equipment and also in AC & DC circuits.
The advantages of absolute solid core mainly include high reliability, mechanical life is longer, heat resistance is good, higher power whereas the disadvantages are dynamic noise is high, moisture resistance is poor, accuracy is poor, the temperature coefficient is large & manufacturing process is complicated.
Metal Glaze Absolute Encoder
The matrix composition of this type of encoder is ceramic, whereas the resistor body is designed with sintered metallic glass glaze. This encoder is made with vacuum technology by arranging different materials like metal oxide film, metal composite film, button oxide film, metal alloy film on a ceramic substrate.
The advantages of this encoder include high resolution, less noise electromotive force, etc. The disadvantages are resistor value is small that ranges from 10 ohms to 00 kilo-ohms, mechanical life is less, wear resistance is poor, etc.
Winding Absolute Encoder
Winding type can be designed by using nickel-chromium alloy wire or constantan wire like a resistor & wounded on an insulating frame. This type of encoder is used mainly as a transformer & voltage divider.
The advantages of this encoder include high precision, contact resistance is small, and temperature coefficient is small. The disadvantages are low resistance, the resolution is poor and high-frequency characteristics are poor.
Digital Absolute Encoder
This encoder is a semiconductor IC, used mainly for measurement in 360 degrees of the revolution known as a single-turn encoder. So it is appropriate for audio surround control, home theater system, cable TV equipment & audio amplifier.
The advantages of this encoder mainly include small size, simple to connect, high adjustment accuracy, no noise, software control is easy and its life span is long. The disadvantages are; it is not suitable for harsh and outdoor environments, difficult to overcome the slip while measuring objects within the orbit.
Absolute Encoder vs Incremental Encoder
The difference between absolute encoder vs incremental encoder includes the following.
Absolute Encoder | Incremental Encoder |
It includes a unique code for every shaft position to represent the fixed position of the encoder. | It is an electro-mechanical device, used to change the angular position of the shaft into a pulse or digital signal.
|
These encoders require power while using this device. | These encoders need power throughout the operation of the device. |
Its cost is high as compared to the incremental type. | Its cost is less due to less complex |
These encoders are used in different applications where controlling, monitoring is required like diagnostic imaging, surgical robotics, etc. | These are used in applications where velocity & direction information is necessary
|
Once the power is lost, it doesn’t lose the information of position. | Once the power is lost, the system shows an error. |
Servo Motor Control with Absolute Encoder with Arduino
In this section, let us know how to control a servo motor using an absolute encoder with Arduino. The interfacing diagram of servo motor control with absolute encoder is shown in the figure below.
If this encoder is rotated in a clockwise direction, then the rotation of the servo motor is also in a clockwise direction. Similarly, if this encoder is rotated in an anticlockwise direction, then the servo motor also rotates in the anticlockwise direction. Connections are made as per the absolute encoder wiring diagram shown above. The required components are,
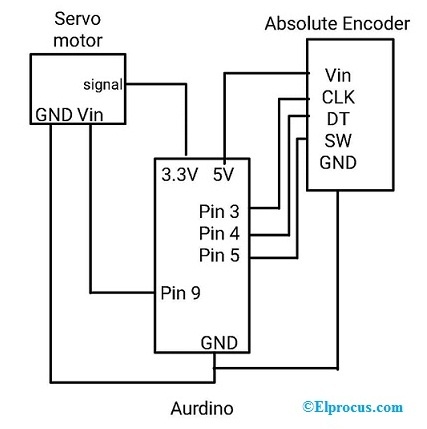
Advantages and Disadvantages
The advantages of an absolute encoder include the following.
- Battery backup is not necessary to avoid data loss.
- They have different functions like scaling, speed, Fieldbus & preset.
Magnetic or optical scan measurement. - Once power is lost, it provides continuous position monitoring.
- The flexibility of programming.
- Interface options are multiple like Ethernet, Analog, Serial, Parallel & Fieldbus.
- Precision control allows use in different applications where functional safety is required.
- The exact position of a machine can be determined.
The disadvantages of an absolute encoder include the following.
- Complicated to manufacture
- Expensive
Comments
Post a Comment